Comprehensive Guide: What is Porosity in Welding and Exactly How to avoid It
Comprehensive Guide: What is Porosity in Welding and Exactly How to avoid It
Blog Article
The Science Behind Porosity: A Comprehensive Overview for Welders and Fabricators
Comprehending the detailed devices behind porosity in welding is important for welders and producers aiming for impeccable workmanship. From the make-up of the base products to the complexities of the welding process itself, a wide variety of variables conspire to either worsen or alleviate the presence of porosity.
Understanding Porosity in Welding
FIRST SENTENCE:
Exam of porosity in welding reveals important understandings right into the integrity and quality of the weld joint. Porosity, defined by the presence of dental caries or gaps within the weld steel, is a common issue in welding processes. These gaps, otherwise correctly dealt with, can jeopardize the architectural integrity and mechanical residential properties of the weld, leading to prospective failures in the ended up item.
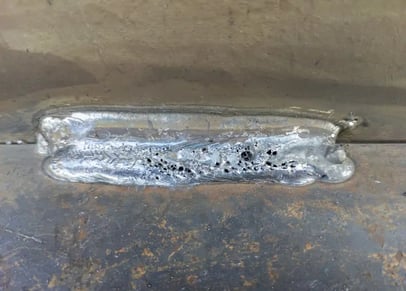
To detect and evaluate porosity, non-destructive testing methods such as ultrasonic testing or X-ray assessment are frequently employed. These methods permit for the identification of internal problems without compromising the integrity of the weld. By analyzing the dimension, shape, and circulation of porosity within a weld, welders can make educated choices to boost their welding procedures and accomplish sounder weld joints.

Variables Affecting Porosity Development
The occurrence of porosity in welding is affected by a myriad of factors, ranging from gas securing effectiveness to the complexities of welding criterion setups. One vital factor adding to porosity formation is insufficient gas shielding. When the shielding gas, generally argon or CO2, is not successfully covering the weld swimming pool, atmospheric gases like oxygen and nitrogen can infect the molten metal, resulting in porosity. Furthermore, the cleanliness of the base products plays a considerable duty. Contaminants such as corrosion, oil, or wetness can vaporize during welding, producing gas pockets within the weld. Welding specifications, consisting of voltage, have a peek here present, travel speed, and electrode type, additionally influence porosity development. Utilizing incorrect setups can create excessive spatter or warmth input, which consequently can result in porosity. Moreover, the welding technique used, such as gas metal arc welding (GMAW) or shielded metal arc welding (SMAW), can influence porosity Recommended Reading development as a result of variants in heat circulation and gas insurance coverage. Recognizing and regulating these factors are vital for decreasing porosity in welding procedures.
Results of Porosity on Weld Quality
The presence of porosity also damages the weld's resistance to corrosion, as the trapped air or gases within the spaces can respond with the surrounding environment, leading to degradation over time. In addition, porosity can hinder the weld's capability to stand up to stress or effect, more jeopardizing the total top quality and integrity of the welded framework. In critical applications such as aerospace, automotive, or architectural buildings, where safety and toughness are critical, the destructive effects of you could check here porosity on weld quality can have severe consequences, emphasizing the value of reducing porosity with correct welding methods and treatments.
Techniques to Lessen Porosity
Furthermore, making use of the appropriate welding criteria, such as the correct voltage, existing, and take a trip rate, is important in protecting against porosity. Keeping a consistent arc size and angle throughout welding additionally helps lower the likelihood of porosity.

Furthermore, selecting the best protecting gas and preserving proper gas circulation prices are vital in reducing porosity. Using the proper welding strategy, such as back-stepping or employing a weaving activity, can additionally aid distribute heat evenly and lower the chances of porosity formation. Finally, guaranteeing correct air flow in the welding environment to get rid of any kind of possible resources of contamination is vital for accomplishing porosity-free welds. By carrying out these methods, welders can successfully minimize porosity and create premium welded joints.
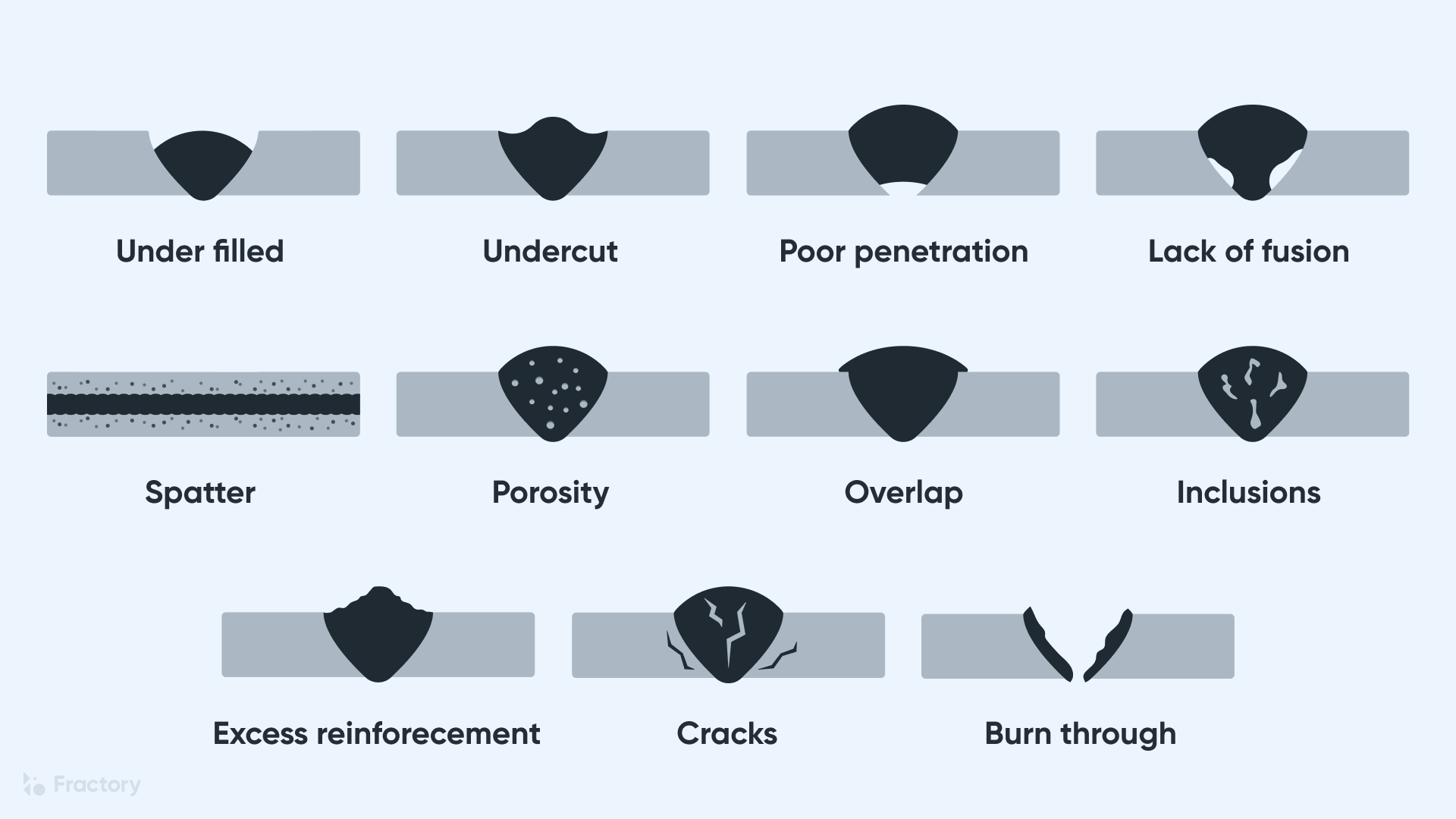
Advanced Solutions for Porosity Control
Implementing sophisticated innovations and cutting-edge techniques plays a critical function in attaining exceptional control over porosity in welding processes. Additionally, utilizing sophisticated welding strategies such as pulsed MIG welding or customized environment welding can also aid minimize porosity issues.
Another advanced service includes making use of innovative welding tools. Making use of equipment with built-in features like waveform control and sophisticated power resources can boost weld quality and lower porosity threats. The application of automated welding systems with exact control over criteria can considerably minimize porosity flaws.
Moreover, incorporating sophisticated monitoring and inspection technologies such as real-time X-ray imaging or automated ultrasonic screening can help in spotting porosity early in the welding procedure, permitting immediate rehabilitative activities. On the whole, incorporating these advanced options can substantially improve porosity control and enhance the total quality of bonded components.
Verdict
In conclusion, understanding the scientific research behind porosity in welding is essential for welders and producers to create top notch welds - What is Porosity. Advanced services for porosity control can additionally boost the welding procedure and guarantee a solid and dependable weld.
Report this page